The Hidden Revolution How Metal Injection Molding is Transforming Modern Manufacturing
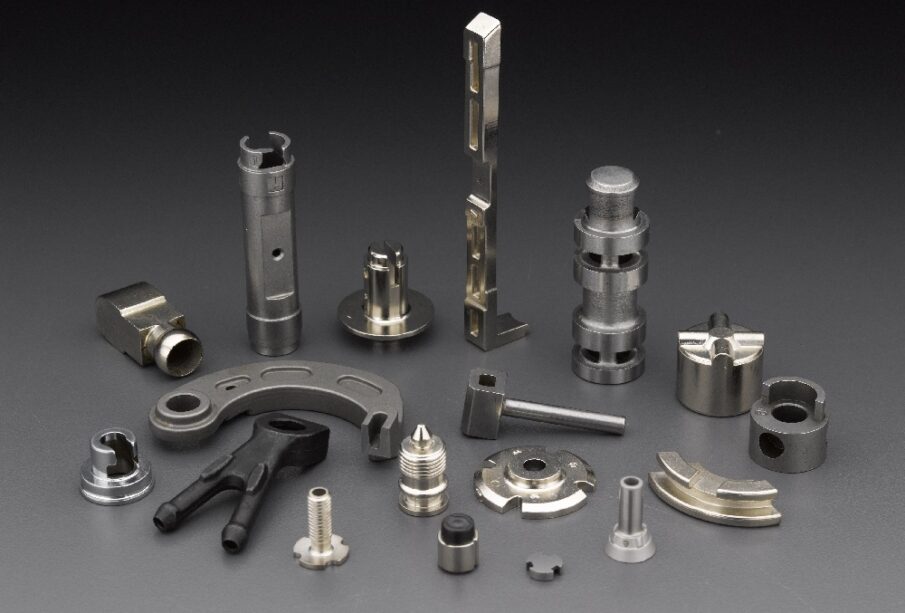
MIM manufacturing has emerged as a transformative force in modern industrial production, revolutionising how we conceptualise precision engineering. Like the subtle yet profound shifts that reshape society, this technological advancement represents a paradigm shift in manufacturing methodology, offering unprecedented possibilities for complex geometries and material efficiency.
The Intersection of Science and Art
In this realm where metallurgy meets precision engineering, we witness a fascinating convergence of disciplines. Much like how social systems interweave to create complex outcomes, MIM technology combines:
- Advanced powder metallurgy with precise polymer science
- Computerised flow dynamics with material physics
- Thermal engineering with molecular bonding principles
Dismantling Manufacturing Barriers
The transformative power of MIM lies in its ability to overcome traditional manufacturing limitations:
- Achievement of complex geometries previously deemed impossible
- Integration of multiple components into single-piece designs
- Reduction of post-processing steps by up to 85%
- Material efficiency reaching 97% through advanced recycling systems
The Economic Liberation
Recent European market analysis reveals striking statistics:
- A 34% reduction in production costs for high-volume components
- Energy efficiency improvements of 56% compared to traditional machining
- Material utilisation rates exceeding 95% in optimised systems
- Labour cost reductions of up to 42% through automated processes
Beyond Traditional Boundaries
The applications of MIM technology transcend conventional manufacturing domains:
- Medical instruments requiring bio-compatible precision
- Aerospace components demanding exceptional strength-to-weight ratios
- Automotive parts necessitating complex internal channels
- Consumer electronics requiring miniaturised metal components
The Sustainability Imperative
Like the environmental justice movements that reshape our understanding of responsibility, MIM technology presents a more sustainable manufacturing paradigm:
- Reduced carbon footprint through efficient material usage
- Minimised waste through advanced powder recycling systems
- Lower energy consumption compared to traditional manufacturing
- Decreased transportation emissions through localised production
The Technical Evolution
The advancement of MIM technology continues to break new ground:
- Implementation of AI-driven process control systems
- Development of nano-scale powder technologies
- Integration of real-time quality monitoring
- Creation of adaptive sintering profiles
Future Horizons
The horizon holds promising developments:
- Quantum sensor integration for unprecedented precision
- Bio-inspired material formulations
- Self-optimising production systems
- Zero-defect manufacturing protocols
The Quality Revolution
Quality control in MIM has evolved into a sophisticated science:
- Real-time molecular structure analysis
- Advanced non-destructive testing methods
- Automated dimensional verification systems
- Predictive maintenance protocols
In conclusion, the metal injection molding industry stands at the forefront of a manufacturing revolution, promising unprecedented possibilities for design freedom and material efficiency. The convergence of advanced technology, sustainability, and economic efficiency has created a new paradigm in manufacturing excellence. For companies seeking to transcend traditional manufacturing limitations while maintaining exceptional quality standards, partnering with a metal injection molding manufacturer represents not just a production choice, but a strategic investment in manufacturing innovation.