How Often Should You Replace Your Warehouse Floors?
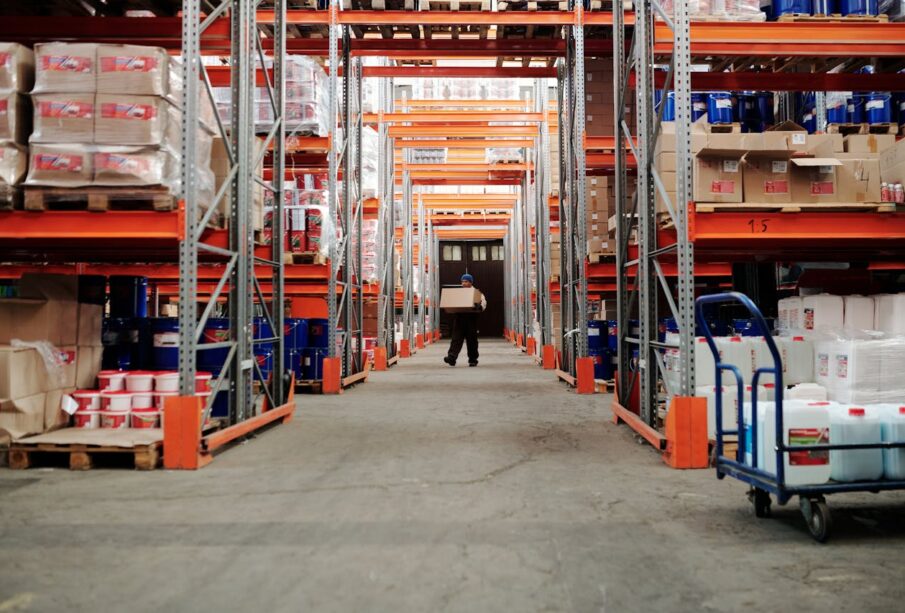
The condition of your warehouse floor is crucial for ensuring a safe and efficient work environment. However, determining the right time to replace your warehouse floor can be challenging. Here are some factors to consider and guidelines to help you make an informed decision about floor replacement.
1. Assess the Current Condition
Regular inspections of your warehouse floor are essential. Look for signs of wear and tear such as cracks, chips, and uneven surfaces. Pay attention to any areas that pose a safety risk, like those that cause tripping hazards or hinder the movement of machinery. If you need to replace it, consider industrial flooring UK from PSR Industrial Flooring.
2. Consider the Age of the Floor
The age of your warehouse floor is a significant factor. Most concrete floors can last between 20 to 30 years, depending on the level of traffic and maintenance. If your floor is approaching this age range, it may be time to consider replacement, especially if it’s showing visible signs of deterioration.
3. Evaluate the Type of Flooring
Different types of flooring have varying lifespans. Concrete, epoxy, and vinyl are common choices for warehouses, each with its durability:
- Concrete Floors: Typically last 20-30 years with proper care.
- Epoxy Floors: Generally last 10-20 years, depending on the thickness and quality of the epoxy.
- Vinyl Floors: Usually need replacement every 10-15 years, depending on the traffic and maintenance.
Understanding the expected lifespan of your specific flooring type can help you plan for replacements.
4. Monitor Traffic and Usage
High-traffic areas and sections subjected to heavy machinery and equipment tend to wear out faster. If your warehouse sees constant movement of forklifts, pallet jacks, or heavy goods, the floors in these areas will degrade quicker. Regularly assess these high-traffic zones for damage and consider more frequent replacements.
5. Review Maintenance Records
Consistent maintenance can extend the life of your warehouse floor. Review your maintenance records to see how often repairs and touch-ups have been necessary. Frequent repairs may indicate that a full replacement is more cost-effective in the long run.
6. Check for Compliance with Safety Standards
Safety standards and regulations evolve over time. Ensure that your warehouse floor complies with the latest safety standards. If the current flooring is no longer compliant, replacing it may be necessary to avoid potential fines and ensure the safety of your employees.
7. Evaluate Operational Downtime
Consider the impact of floor replacement on your operations. Plan replacements during periods of low activity to minimise disruptions. While this might not directly affect the frequency of replacements, it’s essential to balance operational needs with maintenance schedules.
8. Cost-Benefit Analysis
Conduct a cost-benefit analysis to compare the costs of ongoing repairs versus a complete floor replacement. While replacements can be expensive, the long-term benefits of a new, durable floor might outweigh the continuous costs of repairs and potential accidents due to floor damage.
9. Consult with Professionals
Finally, seek advice from flooring professionals. They can provide expert opinions based on your specific warehouse conditions and help you determine the optimal time for a replacement.
Conclusion
Replacing your warehouse floor is a significant investment, but it is essential for maintaining a safe and efficient working environment. By regularly assessing the floor’s condition, considering its age, type, and usage, and consulting with professionals, you can make an informed decision on when to replace your warehouse floor. Remember, proactive replacement can save costs in the long run and contribute to a safer, more productive warehouse.